July 16, 2012
![]() |
BILL KIERNAN |
In agriculture, improving yield per acre and more efficient labor utilization is more important than ever. In a world that needs 70% to 100% more food by 2050 just to provide for population growth, we must reap the most possible from the arable land available, and do it with fewer people. Between the aging of farmers, global urbanization, political squabbles over immigration and the lack of people willing to do the back-breaking field work for the wages that farmers can afford, we simply won’t have the manpower we will need to accomplish this. A possible solution to this dilemma: farmer-robots.
Growing up in the 1960s and 1970s, my mental image of a robot was always this one:
“Danger Will Robinson!”
Today these 1960s robot fantasies are becoming reality, partially driven by the need to feed ourselves.
The need to grow more food, or produce better textiles for instance has pushed humankind to either develop new technologies or adapt existing technologies to achieve that end. Technological adaptation continues today with “swarm technology” or “precision farming” using robots. Agriculture has historically striven toward the bigger and the better; bigger machines to work bigger fields. Today people like David Dorhout of Dorhout R&D LLC believe that the next technological advancements in agriculture will be on the micro-level. Instead of massive machines, we may employ multiple smaller machines working on each individual plant to maximize yield and production.
Dorhout has developed a robot he calls Prospero. Using game theory and swarm behavior algorithms, Dorhout predicts that future farming will be accomplished by swarms of Prosperos who will plant, tend and harvest crops by optimizing yield at every inch of a field. Prospero is an off-the-shelf, low-cost (about $8) robotic platform. Dorhout wrote an advanced walking program that enables Prospero to move in any direction, then added a sensor array, LEDs in its belly, a photo resistor, seed hopper and fertilizer sprayer apparatus and turned it loose.
The end result of his efforts is a swarm of robots that can “talk” to each other using radio signals, and can “see” directly below themselves. If a robot senses that a seed is not planted in the soil below, it drills a hole to the optimum depth, plants a seed, sprays it with the exact amount of fertilizer needed, covers it and marks the spot with a dot of “paint” that Prospero’s fellow robots can detect. A swarm of robots would all be doing this simultaneously, and if a robot finds a large unplanted area, it can call other robots over to help it plant. Using this technology, Dorhout says a field can be planted with optimum seed depth and distance without wasting fertilizer or effort. Expanding on this, other swarms of robots could be modified to tend fields throughout the growing season, monitoring for weeds, pests, diseases and soil moisture.
In the fruit and vegetable industry, most crops must be tended and picked by hand. In more developed countries, it is becoming increasingly difficult to find workers to do this seasonal work at wages that farmers can afford. In Japan for instance, strawberries often rot because they are becoming too costly to pick. In the U.S. immigration laws and political posturing are severely taxing our fruit and vegetable farmers with legal badgering of offshore labor.
Supermarkets prefer fruit and produce to be of uniform size and ripeness. This is difficult to achieve when harvesting entire fields or orchards at the same time. At the Massachusetts Institute of Technology (MIT), experimental crops of tomatoes have been grown tended entirely by robots. Each plant is equipped with a sensor that tracks its condition. If a plant is too dry, a robot is called to water it. When a tomato reaches the perfect ripeness, a robot using vision sensors comes and picks only that tomato. Fruit and produce growers can now program robots to scout and pick only the fruit or vegetables that meet certain requirements; by harvesting over time as each item reaches perfect ripeness, it gives the markets the desired uniformity while reducing waste encountered when harvesting an entire field at one time, therefore increasing profits.
Vision Robotics of San Diego is developing vine pruning robots, and apple and orange picking robots with multiple arms. In Japan, automation of one of the more challenging crops to grow is being developed. Because strawberries develop and ripen in such a staggered manner and go through several shades of red before becoming fully ripe automation has been difficult. Researchers at Miyakazi and Kyoto Universities are now growing strawberries in raised beds being tended entirely by robots. Precise vision sensors signal the robot to pick only the ripened strawberries, cutting them from the vine and holding the berry with suction; then transferring the berry to a conveyor belt for packing and shipping.
Though many of these “agribots” work much slower than humans, they are able to work around the clock – never taking a break or sleeping, more than making up for the differences in work rates. In the future, additional technological solutions can now be considered when discussing how to feed the world. Increasing area of land under cultivation and improving yield have always been prime considerations in increasing productivity, and now also, thanks to entrepreneurs like David Dorhout, efficient use of time and effort through technology is a viable option.
To see a video about swarm technology and Prospero
To see a video about the work being done at the University of Illinois developing robot weeders
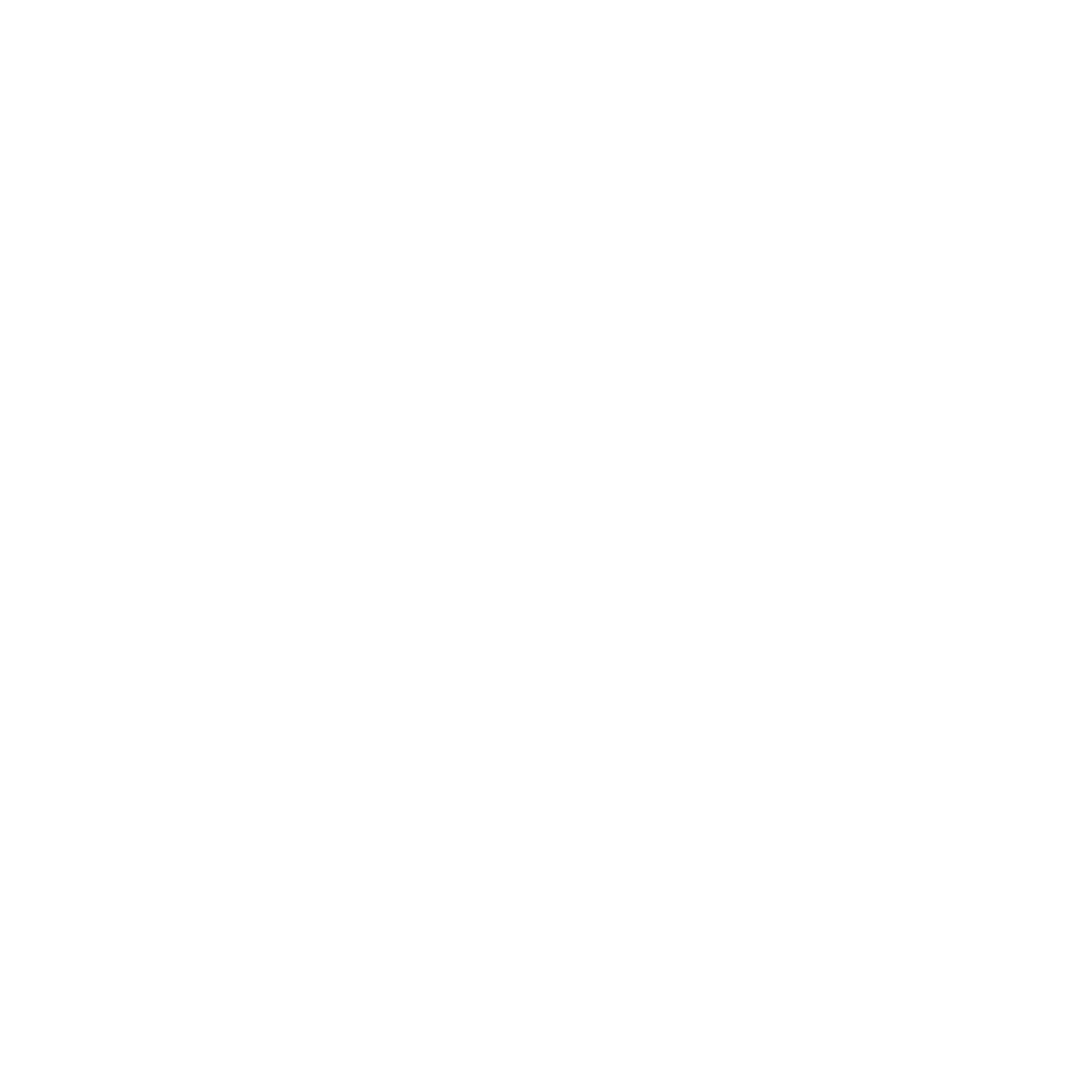
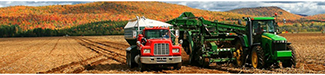
Let GAI News inform your engagement in the agriculture sector.
GAI News provides crucial and timely news and insight to help you stay ahead of critical agricultural trends through free delivery of two weekly newsletters, Ag Investing Weekly and AgTech Intel.